Important Things to Keep in Mind While Manufacturing Plastic Bottles in India
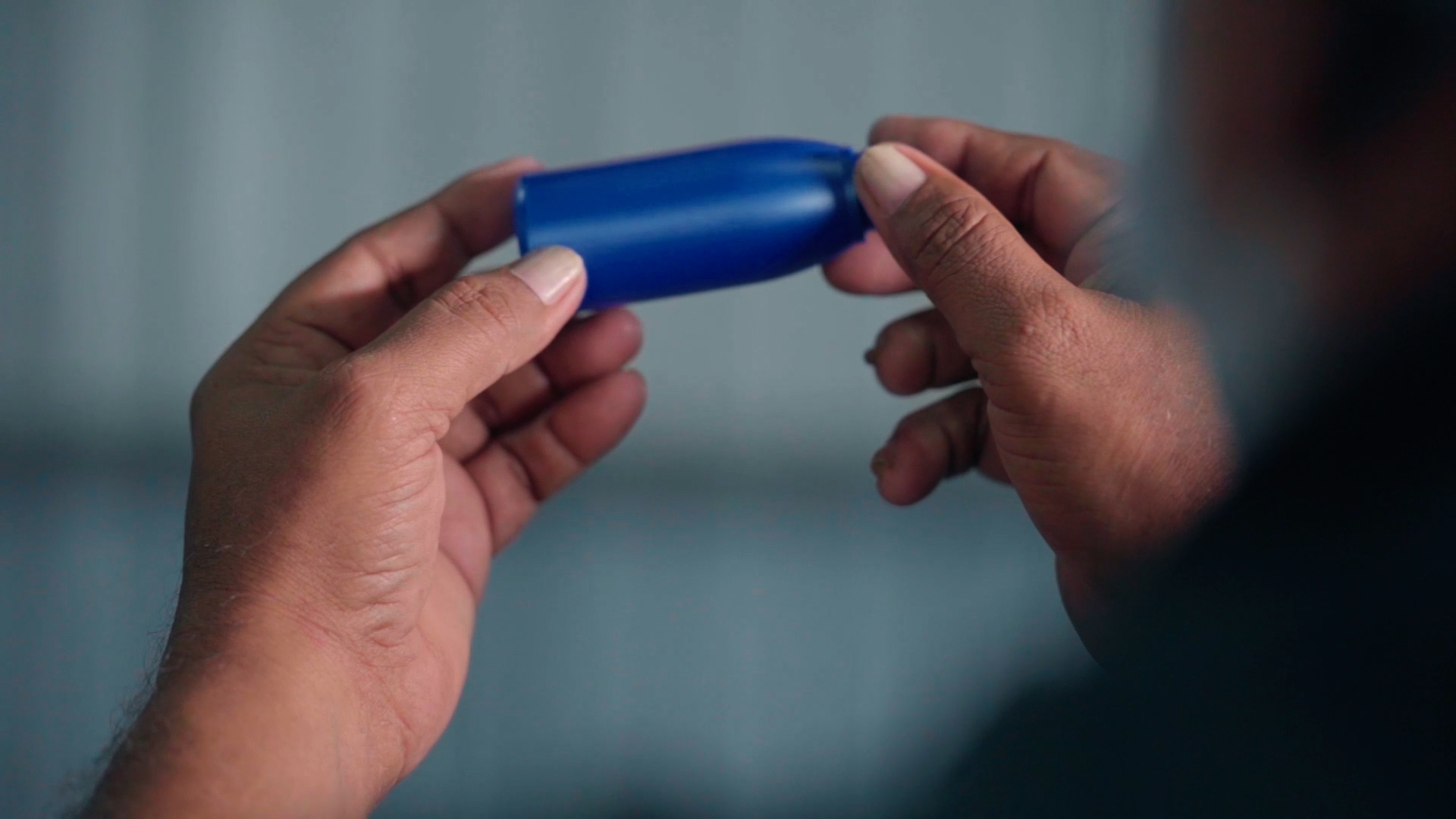
With the growing demand for packaged items like cold drinks, water and juices, India has grown into one of the largest producers of plastic bottles in the world.
From food & beverages to pharmaceuticals and cosmetics, plastic bottles are used across different industries and sectors.
During the manufacturing of plastic bottles, several factors must be carefully considered to ensure the quality and safety of the bottles.
Let us explore some of the important aspects that every manufacturer of plastic bottles must take care of
How To Improve Manufacturing of Plastic Bottles in India
- Conclusion: Improving the Quality as a Manufacturer of Plastic Bottles in IndiaChoosing the right material: The first and foremost thing is to select the right kind of material for any manufacturer of plastic bottles. The quality of the material decides the durability, reliability, functionality and safety of the end product.
The most commonly used materials in the manufacturing of plastic bottles are PET (Polyethylene Terephthalate), HDPE (High Density Polyethylene) and PP (Polypropylene).PET is usually preferred for water and other kinds of beverages because of its light weight, strength and transparency.While HDPE is used to store non-food products due to its high chemical resistance.
- Meeting the safety and regulatory standards: An ideal manufacturer of plastic bottles must comply with all the safety and regulatory norms to ensure safety, quality and hygiene.
When it comes to food & beverages, the manufacturer must ensure that the materials used do not react and produce harmful substances. This way, a manufacturer can enhance its reputation in the market.
- Design & Functionality: It is very important for a manufacturer to understand that a plastic bottle should be functional as well as visually appealing.
Not only should it be easy to use, but also be durable and must avoid leaks of any kind. In a cluttered marketplace, the design is what separates one brand from the others.
- Manufacturing process: The manufacturing of plastic bottles involves two techniques: injection moulding and blow moulding.
First, we create the preform of the bottle using injection moulding, and then it's heated and expanded in the required shape with the help of blow moulding.
For a smooth manufacturing process, a manufacturer must invest in advanced machinery to produce high-quality plastic bottles with relatively fewer defects. It also reduces the turnaround time and leads to increased productivity.
- Cost Efficiency: In a market where there is cut-throat competition, an ideal manufacturer of plastic bottles should be cost-effective without compromising on quality. It involves reduced wastage of raw materials and a streamlined supply chain.
- Sustainability: Plastic is one of the major causes of pollution in the world and with the rising issues of climate change, it poses one of the biggest threats to the manufacturers of plastic bottles.
And that is why, the manufacturers of plastic bottles must adopt sustainable practices like producing recyclable bottles, using recycled materials and reducing energy consumption.
- Quality Check: One of the most important aspects in the manufacturing of plastic bottles is controlling the quality of the end product.
These bottles must pass all kinds of durability and reliability tests. Some commonly known quality control tests are tensile strength tests, leakage & spillage tests and cap fit tests.
An ideal manufacturer must have a dedicated quality control team to ensure that only the best reaches the consumers.
.jpg)
Conclusion: Improving the Quality as a Manufacturer of Plastic Bottles in India
In India, the Manufacture of Plastic Bottles needs coherence in all the above-mentioned aspects to manufacture the best quality plastic bottles.
By checking on all these aspects while manufacturing, an ideal manufacturer can improve the entire process making it profitable and can also contribute to the growth of the plastic bottle manufacturing industry.